Staying Connected
A stable and reliable Internet connection is an important requirement for us. We both often work while on the road. We also travel with our beagle Cappi and need to be in control of her environment when she has to stay behind. After a fair amount of research I decided to install a WiFi Ranger setup. The system includes two routers. One router is mounted inside the van and provides cellular access and anLearn More
Upgrading and Reconfiguring the AC Circuits
For several years now I’ve been running a Victron Quattro Inverter that is capable of handling 30A of AC input and 30A of AC output. Unfortunately the stock wiring and breakers to and from the inverter were only capable of safely supporting 20A. To accommodate the stock components I’ve been programming the inverter to restrict itself to 20A of AC input and output. I found a few hours today to remove that bottleneckLearn More
Managing Rust
Every few months I inspect the chassis to make sure that all is well. During my most recent inspection I noticed a little bit of rust developing on one of the seatbelt washers in the trunk. When I looked beneath the trunk the bottom of the bolt had some rust too. I ordered the following parts and replaced the old hardware today. 1/2-13 x 2-1/2″ 304 Stainless Steel Hex Head Cap Screw Bolts 1/2-13 316Learn More
Adding Awning Supports to Our Carefree Freestyle Awning
The Carefree Freestyle awning on our 2017 Pleasure-Way Lexor TS is very convenient to extend and retract. It’s nice to be able to get a little quick shade without any effort or having to deploy supports. There are times, however, when that convenience becomes a liability. The wind can quickly become your enemy. The motion sensitive automatic retraction mechanism seems to be either too fast or too slow to do its job. I foundLearn More
Our Bathroom Faucet Fix
The bathroom faucet on our 2017 Lexor TS worked but there was room for improvement. It was a standard plastic RV diverter faucet that allowed very little clearance from the edge and bottom of the sink. It also had separate handles for hot and cold water. The search for a replacement was harder than I thought it would be. A brass diverter faucet with a single handle didn’t exist. I finally came across the fixtureLearn More
RAM Promaster Audio System Installation
The standard Uconnect head unit on our RAM Promaster based Pleasure-Way RV left a lot to be desired. It had poor audio quality and its built-in navigation system was inaccurate, slow and difficult to program. I also felt like I needed to learn Klingon to use its built-in voice command system. I had found a way to enhance the navigation capabilities by docking an iPad in our new Dash Clipboard Replacement but the other issues were stillLearn More
Our Plumbing Heating System
We purchased our 2017 Pleasure-Way Lexor TS in Florida in early February. As we headed home to Virginia we realized that our time of enjoying a fully functioning vehicle was running short. Temperatures in Virginia often drop below freezing in the winter and our plumbing system was not designed to operate at sustained temperatures below freezing. I decided that I didn’t want “winterization” to be a part of my ownership experience so ILearn More
Bouncing the Bounce with a VB-Air Suspension
The rear sofa seat belts were a feature that we viewed as a real plus when we decided to purchase our 2017 Pleasure-Way Lexor TS. Unfortunately we quickly found out that they were really just safety restraints for an amusement park ride. While watching our passenger’s get launched in the air each time the vehicle hit a bump was somewhat entertaining we knew something had to be done. The rear seat was basically unusable whileLearn More
Curtain Track Hooks
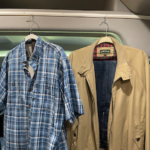
In our 2003 Westfalia camper we had installed some wonderful small hooks at various points around the van that were really handy to hang a towel or clothing from every once in a while. Our 2017 Lexor TS had a closet which was nice but not ideal for anything that might need to air out. We installed some hooks in the bathroom for our towels and washcloths but felt the need for moreLearn More
Building a Solar Panel Rack
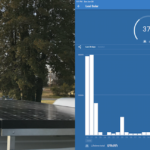
I had just finished installing our new 48V house system and we were leaving in two days for a month long trip to Canada. The two original and now incompatible 12V solar panels were still on the roof and had nothing to do. I had purchased an extra Panasonic 330W 60V panel when I set up the 48V test system in our shed. I decided it was time to put it to work.Learn More